
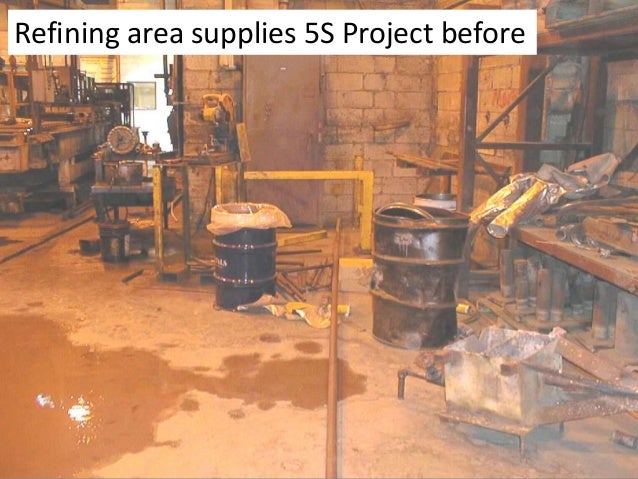
In reality, value stream mapping is far more advanced than this, but this basic information is enough to visualize the processes to analyze them for potential kaizen.
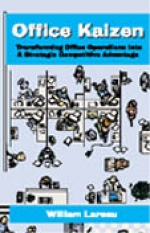
A very simple value stream map would look like this: Each box represents a process, that is, a task that is performed to create the value stream. Once the item of value has been identified, the process to create that value is mapped.

For example, the purchase of a new forklift which optimizes two or more production stations would be flow kaizen. It optimizes the flow of the production system and performs waste removal activities on the overall value stream. Types of KaizenĪlso called system kaizen, this type of kaizen focuses on the overall value stream. Anything that is not absolutely necessary for the creation of the product of value is considered muda (waste) and must be eliminated. Kaizen, translated as continuous improvement, involves the removal of waste from the value stream. In a lean facility, the components of the manufacturing process that produce value (the “value stream”) are identified, and everything that is not absolutely necessary to produce that value is considered muda, japanese for waste. Kaizen is a component of Lean Manufacturing which involves the steady, systematic removal of waste from the production line.
